Challenge
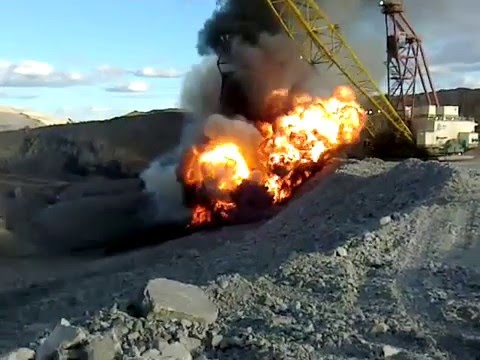
Issue:
Due to the hash mining environment of draglines, the clients current seal that were already worn out was unable to protect the bearings from seizures. It is unsafe when mining seals are worn out as they would not be able to fully protect the bearing.
When bearings fails, it may ignite a fire which can lead to catastrophic results. For example, fire explosions. Fires caused in mining draglines are caused by bearings which are overheated, over greased or a failing seal that causes extra friction due to debris.
Solution
Oz Seals designed and manufactured a custom labyrinth seal for our customer. The labyrinth seal was specially formulated from Oz Seals own range of super polyurethane – Oz Super 95. Proven to outlast even the equipment they seal, the Oz Super 95 has high temperature resistance of up to 150°C.
Oz Seals added a low-cost solution to the seal design – custom bump stops to reduce friction and for the seal to run smoothly. Oz Seals also added an outer lip to the labyrinth pattern design. The additional outer lip – flings out/away contaminants and debris under the rotation which helps to prevent the bearing from failing.
Results
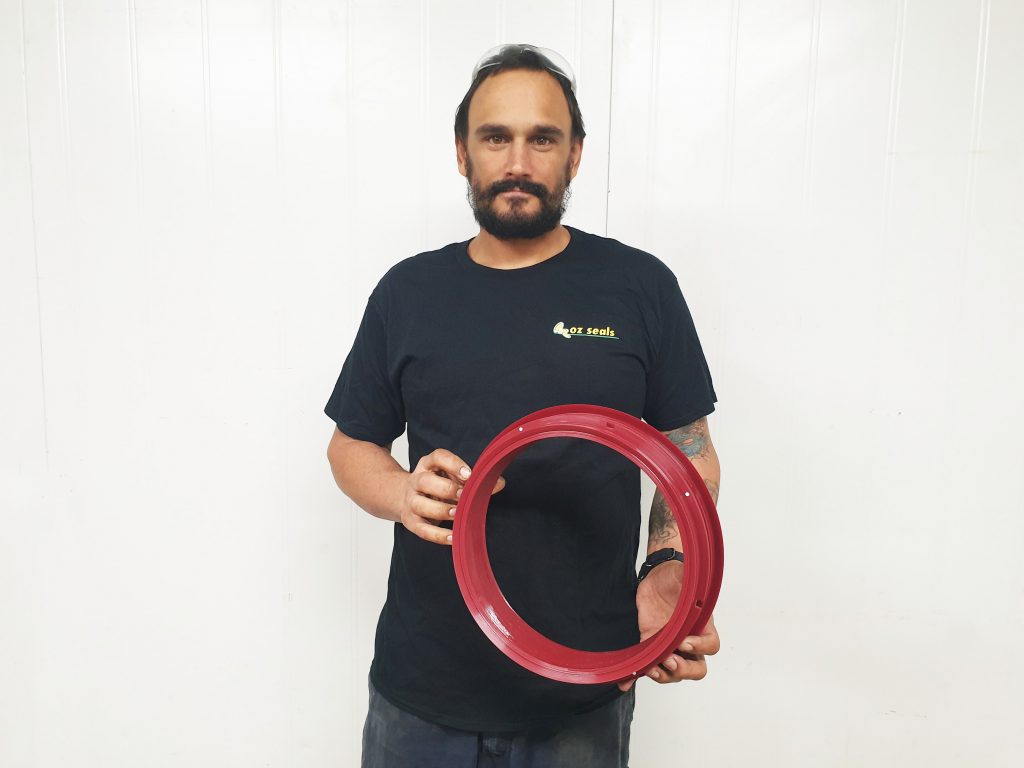
Client Reported:
- The labyrinth seal is working well under harsh mining conditions and is still continuing its service
- The Oz labyrinth seal is performing extremely well in comparison to the previous seal.
- Savings realised due to production downtime, maintenance time and replacement.